
A Better Process Backed by 70+ Years of Experience
The investment casting process or lost wax process, can produce the most intricate shapes in just about any alloy. There is no other metal working process that provides the design freedom to easily cast complex intricate shapes and assemblies as the investment casting process. The lost wax method outperforms any other casting process when it comes to superior surface finishes especially when compared to sand casted, forged or welded fabrications. Moreover, Thompson Investment Casting has 70+ years of investment casting experience working with all types of alloys in all types of industries.
Investment Casting Benefits

Reliability
The investment casting process provides reliable process controls and repeatability that are maintained from casting to casting.
Tolerances
Thompson Investment Casting routinely holds to tolerances of +/- .005” inch per inch, with a typical surface finish of 125 RMS. To achieve tighter tolerances TIC has built an in-house CNC shop.

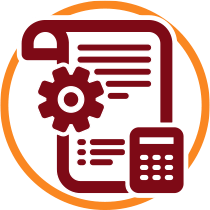
Amortization Lowers Tooling Cost
The initial wax injection mold to produce the patterns, averaged over the entire production quantity, is often lower than other casting tooling costs. Quality tooling produces a quality part and will be more cost efficient in the long run.
Better for the Environment
An investment casting is produced from wax patterns which in most cases can be reclaimed and used again. The wax pattern is a great way to see your part before it is cast, saving valuable time when revisions are needed. More importantly, the investment casting process produces parts to net or near net shapes which significantly reduces or eliminates the amount of secondary machining. Most scrap from secondary services like machining can be reused as well.


Design & Casting Versatility
Thompson Investment Casting works with over 100 different ferrous and non-ferrous casting alloys. This allows our investment casting process to be used in a variety of industries as it produces a wide range of cast and casting based assemblies. Lost wax castings provide the maximum design flexibility for manufacturing complex, multi part products in many cases.
Intricate Design
When using investment castings, design engineers can easily incorporate features such as logos, product IDs/numbers, and letters into their component. Thru holes, slots, blind holes, external and internal splines, gears, and thread profiles can often be cast to reduce secondary machining time and total part cost.
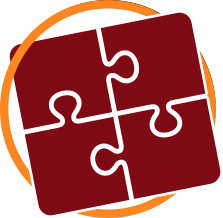
Compare Casting Techniques
Metal Casting Comparison Chart | |||||
Sand Casting | Permanent Molding | Die Casting | Ceramic & Investment Casting | Thompson Investment Casting | |
Dimensional Tolerances | ±.010″ ±.030″ |
±.010″ ±.050″ |
±.001″ ±.015″ |
±.010″ ±.020″ |
±.003 per inch Premium |
Relative Cost – High Part Quantity | Low | Low | Lowest | Highest | Medium |
Relative Cost – Low Part Quantity | Lowest | High | Highest | Medium | Medium |
Casting Weight Range | Unlimited | oz. – 100 lb | oz. – 75 lb |
Ceramic – 3-350 lb. Investment – oz. – 100 lb |
Less than 1 oz to 25 pounds |
Minimum Wall Thickness | 1/10″ | 1/8″ | 1/32″ | 1/16″ | .020″ |
As Cast Finish (RMS) |
150 – 350 | 150 – 200 | 63 – 90 | 60 – 125 | 60 – 125 |
Draft Angle (Degrees) |
1 – 5 | 2 – 4 | 1/2 – 2 | 1/4 – 1/2 | =/- 1/4 to 1/2 |
Design Complexity/Detail | Fair-good | Fair | Good | Best | Best |
Relative Ease of Design Changes In Production |
Best | Poor | Poorest | Fair | Good |
Castable Alloys | Most Ferrous / Non-ferrous Metals | Al-base & Cu-base Preferred | Al-base Preferred> | Most Ferrous / Non-ferrous Metals. |
Ferrous, Copper and Copper Based, Cobalt Based, Nickel Based, Aluminum Based |